Cold Spray Additive Manufacturing (CSAM) of Launcher Propulsion System Components
- Impact Innovations
- May 5, 2021
- 6 min read
Jan Kondas(1), Reeti Singh(1), Max Meinicke(1), Leonhard Holzgaßner(1), Iain Waugh(2) (1) Impact Innovations GmbH, Bürgermeister-Steinberger-Ring 1, 84431 Rattenkirchen, GER (2) Airborne Engineering Ltd., Westcott Venture Park, Aylesbury, HP18 0XB, UK
Present work reports the feasibility of CSAM for manufacture launcher system components with outstanding mechanical properties, large dimensions, and specific geometrical complexity to demonstrate the CSAM process's potential as an innovative process for additive manufacturing. The demonstrated CSAM process has a fast production rate and minimum dimensional limitation leading to high component flexibility. The CSAM process is also suitable for various metals and alloys and their combinations due to the simple dissimilar material joining. The post-heat treatment resolves the issues associated with anisotropy and ductility, resulting in enhanced mechanical properties required for various applications. The high deposition rates make the process cost-effective and suitable to manufacture large components in a reasonable time frame.
CSAM is also a potential technique considered for adding structural parts, such as manifolds or jackets to a conventionally machined or even SLM fabricated liners.
Introduction
In space applications, materials with high strength-to-weight ratios and properties such as excellent tensile strength, fatigue strength, and fracture toughness combined with low density are essential. However, there are specific parts, such as launcher propulsion system components, where the focus of the materials’ properties is on heat conductivity and mechanical strength at elevated temperatures. Furthermore, the main requirement is to join materials with different melting points.
One of the most critical components in the launcher propulsion system is the so-called thrust or combustion chamber, a regeneratively-cooled, convergent-divergent shape chamber. Conventional combustion chamber manufacture starts with casting and forging of a Cu-based high strength and highly thermally conductive alloy such as, GRCop42; GRCop84, NARloy-Z or CuCr1Zr, which usually leads to delivery times longer than 12 months. Once the raw liner part is delivered, it is turned to the required dimensions, and the cooling channels milled to the outer surface of the liner material. Closing the channels is usually done via brazing, electroplating or diffusion bonding. These processes are also used to deposit or form the outer, so-called jacket material which is a higher tensile strength material to reduce engine weight. These processes are very challenging, time-consuming, costly, and suitable only for limited type of metals or alloys. Finally, the inlet manifold must be welded to the combustion chamber, which is a critical process from the thermal and residual stress point of view.
New commercial rocket engines require fast and low-cost AM processes giving sufficient flexibility to react to the changing demand of launches. For these reasons, in the past few years’ significant attention has focused on AM process and developments, particularly to selective laser melting (SLM) due to its design freedom and prevalence on the market. However, SLM
techniques has several disadvantages limiting the utilization and scalability for combustion chamber manufacturing:
Limited build envelope dimensions
Limited processing of metals and alloys
Design limitations, especially the build angles and support structures
High surface roughness, particularly in the cooling channel inner walls, which are almost impossible to polish.
Does not allow to deposit layers of different materials.
The Cold Spray Additive Manufacturing (CSAM) process, developed by Impact Innovations GmbH, has the potential to overcome all the limitations as mentioned earlier and offers a potential solution to manufacture combustion chambers with superior properties and no envelope size restrictions. The CSAM process was already illustrated on several demonstrator components, as shown in the photos. However, the concept of combustion chamber manufacturing had to be verified and tested. For that reason, Impact Innovations GmbH set up a collaborative project with Airborne Engineering Ltd (AEL), a UK based company specializing in a propulsion system design and testing. AEL designed a combustion chamber demonstrator according to Impact Innovations GmbH guidelines for CSAM process possibilities and limitations.
CSAM Demonstrators:
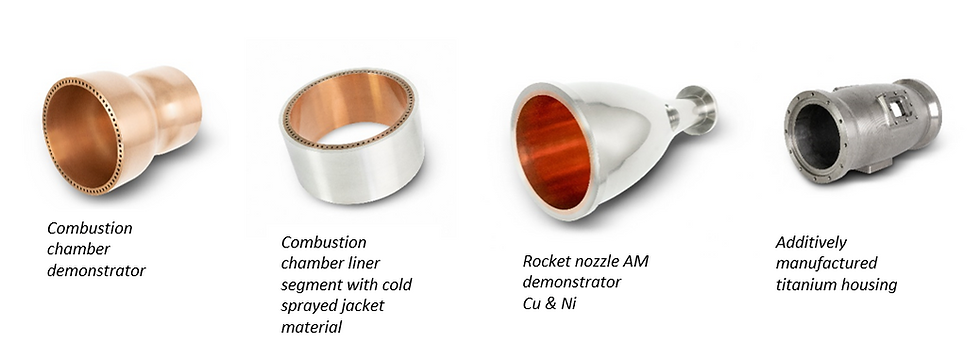
Design

The combustion chamber was designed with a length of approx. 500 mm and the diameter approx. 300 mm. The regeneratively cooled liner is a high-strength Cu-alloy, and the outer jacket material is designed for Inconel. The design includes the inlet manifold, which was manufactured directly during the Inconel jacket manufacturing. The manifold's inlet pipe with a flange was designed to be made separately by CSAM and welded to the manifold additionally.
Cooling Channel Feasibility Trials
In the first step, feasibility to manufacture different cooling channel dimensions was necessary to verify. For that reason, two rings with the bi-metallic design with embedded cooling channels were manufactured. The 280 mm diameter demo sample with a channel width of 1 mm and a channel depth of 5 mm was selected for the smallest channel cross-section verification. The second demo sample with identical diameter and three different channel dimensions: 5x4 mm, 4x3 mm, and 2.2x1.5 mm was manufactured for the wider channels. Both demonstrators were successfully fabricated, and the channel concept verified.
In addition to verifying the coolant channel geometry, the combination of the high- strength Cu-alloy and Inconel jacket was verified, at the maximum diameter and most diminutive channel dimensions. There were no cracks or defects observed on the demo sample.
Manifold CSAM Feasibility Trials

To prove the concept of manufacturing a direct inlet manifold, a third demo sample was designed with identical dimensions as the combustion chamber but manufactured only the inlet manifold area as shown in the right picture. As in the previous cases, the inner regeneratively cooling layer was fabricated using high strength and thermal conductive Cu-alloy, whereas the outer jacket layer and the inlet manifold were with Inconel. The outer diameter of the manifold is 290 mm, the cooling channels were created in the Cu-alloy with ending into the manifold.
The manufacturing steps were consisting of:
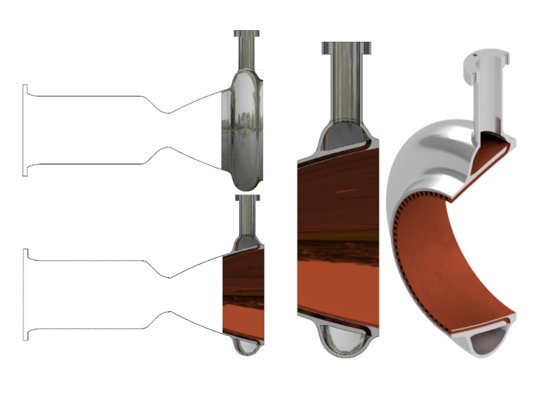
Mandrel manufacturing
Cu-alloy deposition
Cooling channel milling & filling
Inconel jacket layer & manifold deposition
Inlet tube deposition
Mandrel & filler material removal
Heat treatment and inlet tube welding
All these process steps were successfully carried out, and the manifold demo sample manufactured. To verify the integrity and potential crack or defect in the first case, a segment of the manifold demo sample was extracted via wire EDM. The extracted segment shows no crack or any defects.
Manufacturing of both types of feasibility demo samples proved the CSAM process suitably for the combustion chamber manufacturing application and the advantages compared to other additive manufacturing process such as:
No protective atmosphere required.
Simple joining of dissimilar materials/alloys
No thermal stress
No cooling channel surface roughness issues
Access for inspection during production steps
Ability to re-work/repair areas for prototypes
Ability to join additional parts without welding (e.g., injector head, actuator mounts)
Powder is only required for the material to be deposited, rather than in SLM processes where it is required to fill the entire build volume. This could help with qualification, because new powder can be used each time, rather than there being an economic incentive for powder recycling as in SLM processes.

To demonstrate the dimensional flexibility of the process, at Impact Innovations’ spray-lab the spray lathe allows to manufacture components up to Φ1500 mm diameter, 2000 mm length at max component weight of 1500 kg. Presently, a full-size combustion chamber, shown in Picture 3 is under fabrication at Impact Innovations GmbH and soon available for the demonstration and fire testing at AEL site.
Deposition Rates & Mechanical Properties:
One of the most critical aspects of the combustion chamber manufacturing process is materials’ mechanical properties. For that reason, in the conventional manufacturing route, the liner’s starting material is the high-strength Cu-alloy in a casted & forged state. Any further heat treatment leads to grain growth and decreasing the mechanical properties. The advantage of the cold spray process is that it uses fine powder particles with grain sizes below 10 µm, which
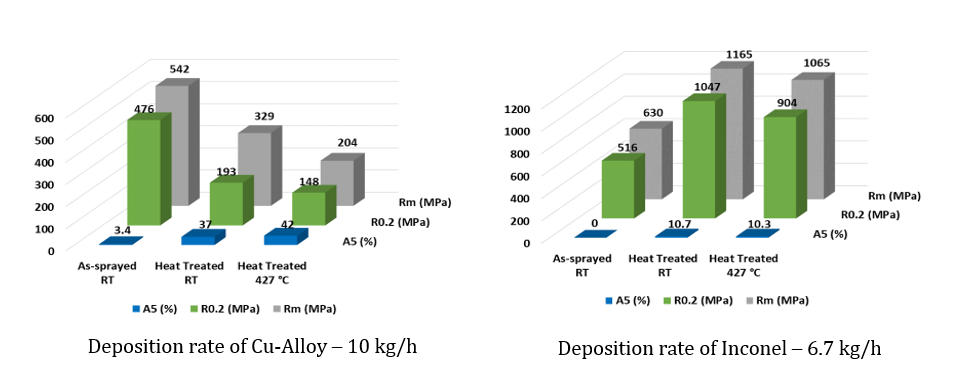
deformed plastically during the process, leading to a fine grain structure of deposits. Fine microstructure of the deposit with many structural defects such as dislocations and vacancies allow heat treatment at higher temperatures, and longer time can be carried out without significant grain growth, degrading the yield and tensile strength of the material. Higher temperatures and longer holding times are required for the Inconel heat treatment. It means that only one heat treatment operation can be carried out on the final combustion chamber, leading to high mechanical strength and ductility. The high-strength Cu-alloy and the Inconel's mechanical properties were tested on a sample manufactured parallel to the cooling channel demo sample. The resulting mechanical properties are shown on the charts, measured in as-deposited state and after heat treatment at room and elevated temperature (427°C).
The second important aspect is the deposition, rate which has a significant effect on the cost. The CSAM process developed by Impact Innovations has a deposition rate of 10 kg/h Cu alloy and 6.7 kg/h deposition rate for the Inconel, which is in comparison with highest available SLM deposition rates more than 20 times faster.
Still Need Help?
+49 8636 695190-0
Commentaires