SPEE3D: Conquering Copper Nickel
- SPEE3D
- Sep 27, 2024
- 4 min read
Updated: Sep 30, 2024
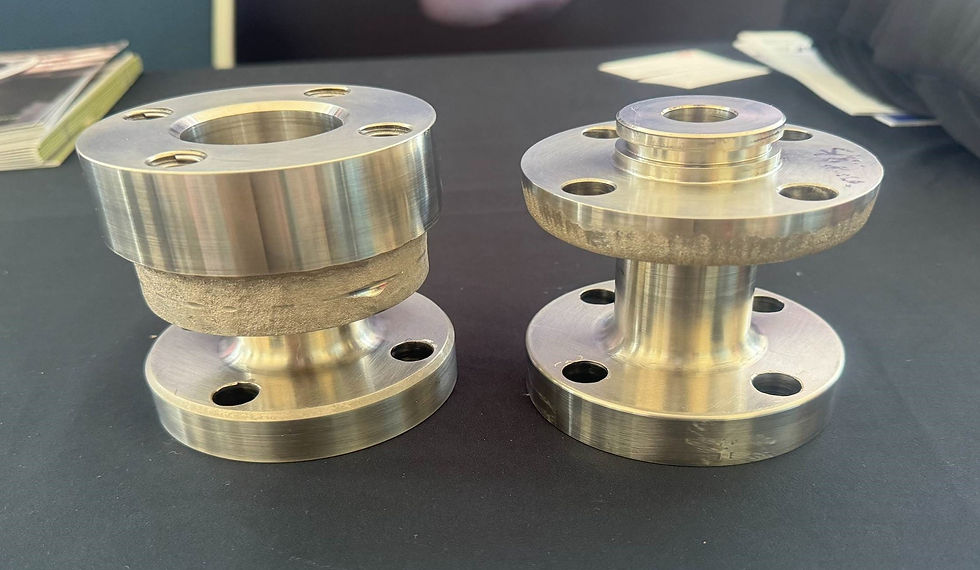
Learn what it takes to develop a new cold spray powder—and how guest blogger
Chase Sheeley is navigating the challenges of additively manufacturing copper nickel.
Chase Sheeley is an Additive Manufacturing Research Engineer at SPEE3D. He completed an MS in Materials Science & Engineering with a thesis on additively manufactured stainless steel—and brings valuable experience in the aerospace and defense industry to his role at the company.
Every day at SPEE3D, we’re looking to expand the possibilities of Cold Spray Additive Manufacturing (CSAM).
And as someone on the frontlines of new material development—SUBSAFE materials, more specifically—I can speak to the challenges research engineers face in qualifying new metals and alloys for production.
Copper nickel is a perfect example.
Naval Sea Systems Command (NAVSEA) had approached SPEE3D with a specific request for a copper nickel alloy. It’s a material they’d worked closely with for almost 70 years because it provides a perfect balance of strength, ductility, and corrosion resistance for vessels and equipment at sea.
At the same time, however, copper nickel castings often have a high fallout rate —and subsequently can’t be created in a foundry without requiring extremely long lead times.
Bringing casting production in-house could effectively help the Navy eliminate those long lead times. Which made CSAM an ideal solution.
But creating the alloy was no easy task.
To understand why, you need to know a little about how cold spray additive is used to create metal parts in the first place.
In a typical cold spray process, feedstock powder is loaded into a SPEE3D printer and sprayed at supersonic speeds onto a substrate. The printed part must then be heated in a furnace—or sintered—to create the desired alloy.
In some cases, a hot isostatic press (HIP) is used to add pressure to the process with gas, evenly applying 30,000psi of force to the part—exceeding the amount of pressure you’d expect to find at the bottom of the deepest part of the sea.
This enables us to close pores in the heated metal, potentially crushing oxides that threaten a material’s ductility, performance, and reliability.
Once heat treated, the part must then be cooled. Leaving it in the furnace to cool slowly or “quenching” it in cold water to quickly lock its microstructure in place are two common methods.
But while the literature is clear about how to print, heat treat, and cool commonly additively manufactured materials like stainless steel, it doesn’t have much to say about copper nickel.
To create a CSAM heat treatment formula for it, we’d need to navigate some uncharted territory.
Our first challenge was the feedstock itself. Unlike other materials, copper nickel feedstock is a blend of pure elements that gets homogenized into a final alloy via the heat treatment process.
To find the right combination of elements, we simply had to experiment—and the success of each experiment couldn’t be determined until each part had undergone heating and cooling. This, naturally, took time.
Additional experimentation was required with the order of operations.
First, we left the heated part in the furnace to cool off slowly, which created huge hardening precipitates in the microstructure and made the part too brittle.
We then tried quenching the heated part to accelerate the cooling process—but in doing so prevented the hardening precipitates from forming in the microstructure.
This made the part too ductile.
In the end, by homogenizing the copper nickel part before applying a hot isostatic press, then regulating the cooling rate to a moderate degree, we were able to strike the right balance of strength and ductility—and create the desired microstructure.
But our work continues.
While we’ve successfully established the correct sequence in which to additively manufacture copper nickel, we remain in the process of providing evidence of repeatability.
Validating the material to mil-spec standards, showing it can pass every validation test, establishing consistent quality dozens of times in a row—it’s an arduous process that can take anywhere from six to 15 months.
Which is to say, there’s much to be done to optimize the process and deliver a material powder that can safely and reliably replace a traditionally manufactured part used in a variety of critical applications.
While copper nickel has been our primary focus, we are continuously exploring new horizons in material science to broaden our capabilities and meet diverse industry needs.
Our roadmap includes the development of binary aluminium bronze and nickel aluminium bronze—each chosen for their exceptional resistance to wear and corrosion, making them ideal for maritime applications. Additionally, we are delving into the possibilities of using stainless steel, known for its strength and durability, to cater to more demanding environments. These materials are being considered for their unique properties that could revolutionize the standards of durability and cost-efficiency in additive manufacturing.
To reach out to SPEE3D directly, contact us here.
Comments