Cold Spray Repair Technologies Reduce Navy’s Supply Chain Delays
- NCMS
- Nov 2, 2022
- 3 min read
In March 2021, one of the largest-ever container ships became stuck in the Suez Canal for six days, bringing sustained public attention to the commercial maritime industry’s importance. The crisis impacted already strained global supply chains and held up an estimated $9.6 billion of trade each day. Because the US economy relies on maritime fleets to deliver vital finished goods and raw commodities to a multitude of industries, any disruption to these fleets causes shipping delays, resource scarcity, and increased prices.
Commercial maritime assets are globally deployed in demanding conditions—both extreme distances and harsh environments—which constrains technicians’ abilities to perform maintenance and sustainment operations while underway. For this reason, maintenance experts, in both public and private sectors, are interested in technologies that can make repairs to vessels at sea. Such technologies would enable ships to continue towards port with critical cargo and to accomplish their missions without delay.
To develop these technologies, in 2020 NCMS brought together a collaboration—Advancing Additive Repair Technologies and Cold Spray for Sustainment of Maritime Assets—that is conducting research and development into additive repair technologies, including cold spray, to reduce maintenance costs, dramatically extend the life of commercial maritime assets, and help keep global supply chains intact to serve the general public. The project combines the expertise of Naval Sea Systems Command (NAVSEA), Naval Air Systems Command (NAVAIR), and the US Marine Corps, along with two industry partners: VRC Metal Systems and Solvus Global, and two academic partners: Kostas Research Institute (KRI) at Northeastern University and Temple University.
Cold spray is a solid-state coating deposition technology that has recently been applied as an additive manufacturing process to fabricate components and to repair damaged components. Its capability to add new metal onto worn surfaces enables critical features to be re-machined back to tolerance, allowing parts previously destined for scrap to be reused. Cold spray provides an incredibly powerful tool for the commercial maritime industry to quickly refurbish an existing damaged or out of tolerance part and simply reuse it, rather than waiting weeks, months, or years in some cases, for a replacement part.
“In the last three to four years, cold spay has become commercially viable,” said Kiley Plooster, Motion Systems Engineering Program Manager at VRC Metal Systems, LLC, where she specializes in setting up facilities to integrate cold spray. She works on preparing equipment, robotics, dust collection, and more.
This project’s first phase demonstrated a variety of cold spray technologies in three Navy shipyards. Additionally, the collaboration’s highly skilled engineers and technicians developed qualified spray procedures (QSPs) to efficiently repair NAVSEA impellers using the KRI Cold Spray Additive Manufacturing Laboratory’s advanced equipment. The team also created a software tool for cold spray professionals that enables them to select cold spray operating conditions and manufacturing costs for a variety of materials used by NAVSEA. Finally, the team developed a cold spray technician training module, which includes information on the fundamentals of cold spray, robotic operation, interactive tests, and more.
Building on these successes, Phase II expanded the demonstration of cold spray technologies into a fourth Navy shipyard to validate the technologies across a wider range of applications. The team also added portable and hatchable cold spray technology to provide in-situ repairs on ships that are underway. Moreover, they investigated the technologies for applicability in coatings while maturing the testing criteria and design for use in structural repairs. The collaboration also developed a workflow for QSP development, including creating digital twins of the damaged parts. Using digital twins before and after repairs reduces the time and effort required inspect the outcome.
“This project and the work that we’re all doing benefits the Navy because the cold spray is quick and effective,” said Plooster. “The Navy is now able to repair parts a lot faster and for a lot less money. Cold spray is especially useful for obsolete parts on everything from helicopters to aircraft carriers, where the original OEMs no longer exist. Instead of having to completely remake the part, we can now repair it.”
The customer is pleased with the results so far and Phase III is in process. This initiative, which is scheduled to wrap up in 2023, will provide a road map for the successful adoption of cold spray and other additive repair technology in the Navy, and will ultimately enable its transition throughout the DOD, onward to commercial maritime companies and fleet maintenance organizations. While the initiative focuses on ships, the results will be applicable to many other industries, such as truck transport, train, aircraft, and other situations where repairs adversely affect deliverables and time schedules.
“A lot of commercial entities are having problems with parts being unavailable, due to COVID-19 and the supply chain issues,” said Plooster. “Having the ability to repair a part that normally would be thrown away is huge.”
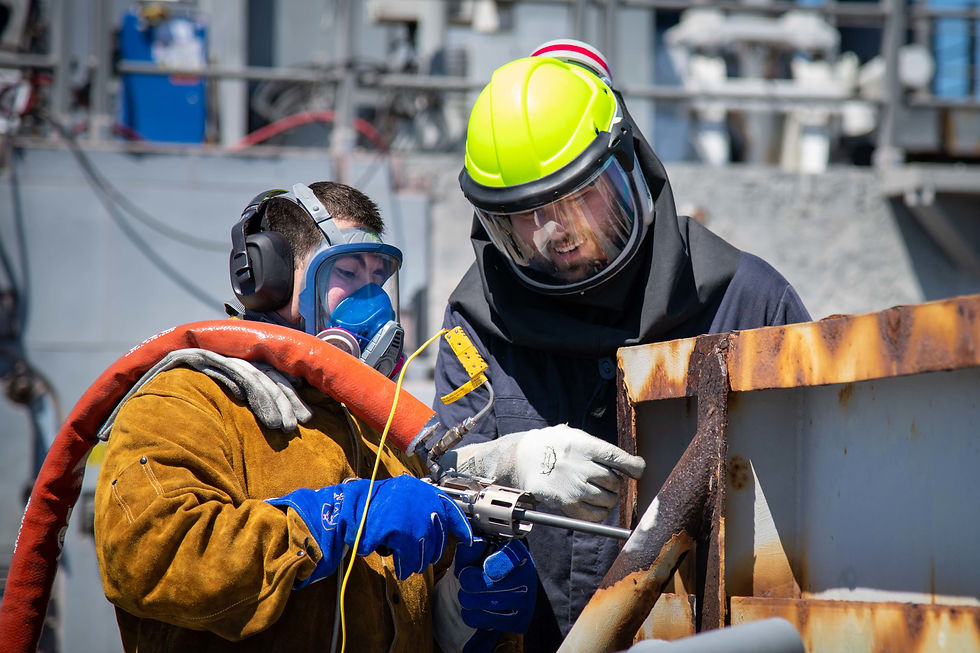
Link to the article on our website:
Link to the article in the complete publication:
Comments