
Cold Spray is a material-deposition process whereby particles of diameters between 1 and 40 microns in diameter are impacted at high velocity onto a substrate. The particles are placed in a gas stream of nitrogen, helium or air. The stream is then heated and accelerated through a de Laval supersonic nozzle at speeds ranging from 1000 to 2500 meters per second. The particle stream is directed towards a substrate, where the particles are consolidated in the solid state.
Overview
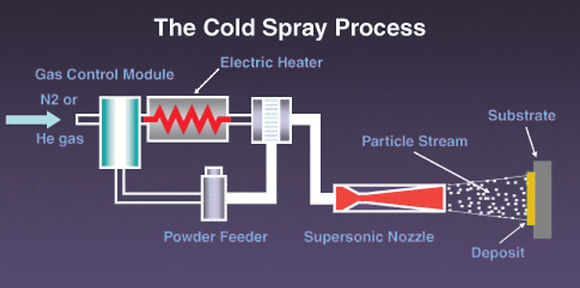
Cold Spray Advantages
Cold Spray offers several advantages over other coating systems and deposition processes. Being a low-temperature process, Cold Spray operates below the melting point of metals, requires no combustible fuels or gases, and results in very low porosity deposits. Its solid-state bonding feature, similar to explosive bonding, allows mechanical mixing of particles and substrate. High velocity impact results in plastic deformation of particles to disrupt oxide films, and provides compressive residual stresses. Cold Spray can also be used to form high-density deposits, producing thick coatings of low oxide and porosity content and/or free-standing structures.
Low Temperature Process
-
Below melting point of metals
-
No combustion fuels, gas
Solid State Bonding
-
Mechanical mixing of particles and substrate
-
Similar to explosive bonding
-
Plastic deformation of particles disrupt oxide films
High Density Deposits
-
Form thick coatings at high deposition rates
-
Low oxide and porosity content (<1%)
-
Form free-standing structures
Compressive residual stresses


